EXPANDING OUR STAR
The star of innovation, Hyundai Sungwoo is
moving towards a new future in the business of
auto parts industry.
DURABLE FAITH
Committed to our promise,
our iron casting business will pursue growth
with the trust of our customers.
SURENESS that MOVES
For optimum stability, our alloy wheel business will take
customer experience to the next level through outstanding
design and technology.
WAY OVER the LIMIT
Surpassing challenges and limits,
our battery business is constantly setting
new standards in the battery industry.
A BETTER TOMORROW
Opening a sustainable future through
new material business, logistics and
integrated purchasing business
-
CASTING
-
ALLOY WHEEL
-
BATTERY
-
ADVANCED MATERIALS
-
CASTING
We are equipped with wide ranges of production lines to fulfill manufacturing from automotive casting materials to industrial products.
-
ALLOY WHEEL
We spare no effort in increasing efficiency of production lines, and pursue innovation while respecting international quality standards.
-
BATTERY
We bring customer satisfaction for a variety of application in the battery industry by way of our unrivaled quality and technological competitiveness.
-
ADVANCED MATERIAL
Alongside the our strong logistics business, we are preparing for a tomorrow to meet the dynamic trends in auto parts business.
Company
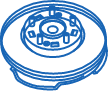
IRON CASTING BUSINESS
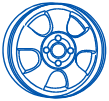
ALLOY WHEEL BUSINESS
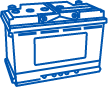
BATTERY BUSINESS
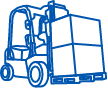
ADVANCED MATERIAL BUSINESS
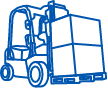
PR Films
- Company
- Vision & Philosophy
- History
- Network
-
-
-
Corporate philosophy rooted in respect for humanity. Mission to satisfy the needs of customers. With our vision and philosophy, we will further enrich lives and enhance technologies.
-
-
-
Our pioneering spirit to venture out and create new paths is the foundation of Hyundai Sungwoo. In the next 10 years, we will envision and practice technology that changes the paradigm of the global market.
-
-
-
Firmly rooted in the spirit of innovation and challenge, Hyundai Sungwoo pursue growth and expansion.
-
We keep challenging towards
a better future for mankind.
The history of Hyundai Sungwoo is
the footprint of the Korean auto parts technology.
Growing as a leading company that
sets new global standards based on
technology innovation.
- Sustainability
- Ethical
management - Environmental
management - CSR
Sustainability
We practice solid and transparent
management to achieve maximum
customer satisfaction.
Growth based on trust is our priority
and promise is the number one
principle and promise Hyundai
Sungwoo Holdings guard with passion.
Sustainability
For future generations, we take initiative to
protect a greener tomorrow..
Hyundai Sungwoo is committed to improving environmental
sustainability. We are pursuing green growth.
Sustainability
For a better world,
we nurture hopes for tomorrow.
As a company dedicated to social responsibility,
we will contribute to positive social change and a
better future.
- PR Center
- PR Material
- PR Films